Fiberglass Pergola Factory Tour
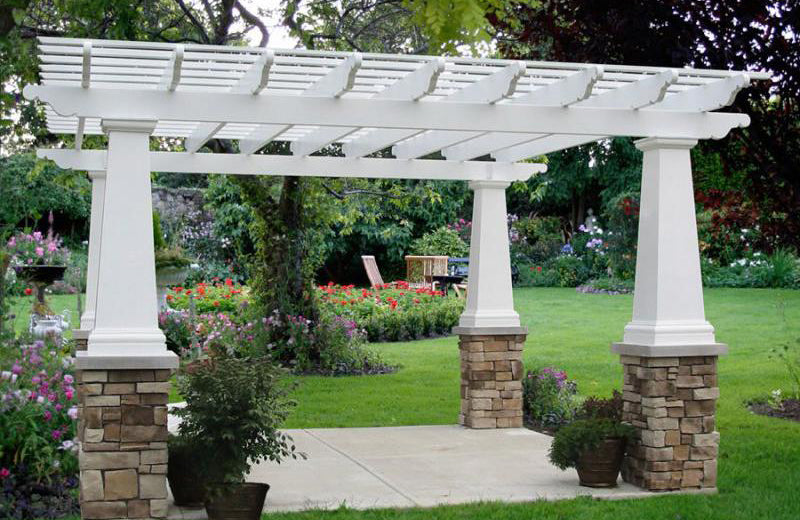
Peaceful Patios Fiberglass Pergola Factory Tour
I recently visited the factory that makes our fiberglass pergola kits and took the opportunity to get some behind the scenes video of our pergolas in various stages of production to give you an idea of the process and the care that goes into making each pergola.
Learn how the pultrusion process creates a pergola that's pound for pound stronger than steel while being lighter than wood and does not expand and contract with freezing and thawing temperates. We also look at how the pergolas are covered with a special formulated coating and packaged in custom built crates to ensure they reach our customers in fantastic shape.
Our various anchoring systems are also shown to give an idea of how we can customize the pergola to resist high wind, mount to a deck, or even use a heavy duty anchor if needed for larger pergolas.
Below is some information gathered while visiting the Peaceful Patio Fiberglas Pergola factory and speaking with George Matthews about what makes this product so unique.
Why are the fiberglass components so strong?
The strength that is within the fiberglass components used for the pergolas comes from the layering of fiberglass mats over and under the fiberglass roving.
- These fiberglass mats have microscopic or tiny little fiberglass strands that are interwoven onto the mat.
- In between the fiberglass roving are hundreds of those tiny fiberglass strands that are all bound together to make a little sort of fiberglass rope.
- When you combine it with the resin, it makes it stronger pound for pound than steel.
What is the process of getting them to come together?
- The process to get them all together is our pultrusion machine and then in the back of the pultrusion machine is a bath.
- This bath holds the polyester resin material.
- The fiberglass roving goes through the bath and then combines with the fiberglass mats around a steel mandrel.
- The mandrel goes into a heated dye with the fiberglass mats and roving.
- The mandrel is what creates the shape of the fiberglass part.
What are some of the benefits of this process for the finished product?
- With this process, there are no issues with temperature changes.
- There is no expansion or contraction changes from the weather.
- This is due to the curing process with the fiberglass and the pultrusion process.
- Once the fiberglass structure is set into that shape, it will not move, compared to vinyl and/or PVC which is malleable once it reaches a certain temperature.
- Our structures have a high heat resistance which makes it perfect for outdoor kitchens, grills and other applications exposed to more heat.
How strong are some components given the thickness?
- A column shaft is 1/8” thick, with the rib piece about ¼” thick.
- Because of the strength to weight ratio, the hollow components can have wiring run through, lighting mounted, electrical sockets, and tubing for gas or water.
- Basically, due to its strength, you can install anything inside or outside of the column shaft.
- When rafter and purlins come off of the pultrusion machine they are hollow rectangular or square tubes.
- They are stuffed on the ends with a high-density urethane foam.
- They are allowed to cure inside, then they hard cut or rout the tail design making it one continuous piece.
- Brackets can be preinstalled to the determined spacing to make installation easier.
- This is usually discussed and quoted during the initial sales process.
How are the pergolas sent to consumers?
- Each pergola is shipped out in a custom-made crate that is built for that particular pergola.
- Hence, all crates look different depending on the size and shape of the pergola ordered.
Are pergolas painted?
- The materials are painted in an aluminum/finished steel chamber which is the painting booth.
- Chromoguard, is a paint coating specifically made for fiberglass outdoor living products.
- It is an acrylic, latex, water-based coating which bonds to the material.
- The coating guards against fading, cracking, chipping and comes with a limited 10-year warranty.
- Once it is cured, it is made ready for shipping.
- The materials will be blown off and wiped down.
- Sleeved together in plastic sleeves.
- Packaged in the crate for shipping.
Are there different anchoring systems available?
- There are different anchoring systems for concrete, wood or composite platforms.
- A ¼” thick, 10” square steel wind load or deck plate can be used on concrete, wood or composite deck applications.
- It’s good to use with concrete because it will give the pergola a higher wind load rating of 165-175 mph versus the standard 70-90 mph.
- Plates that are used on concrete, will be supplied with 4 wedge anchors for each plate.
- No anchors will be supplied if the plates are going on decks since the consumer and professionals will know which anchor will work the best for the deck.
- There are aluminum flush mount rafter brackets fits the nominal 2x8 rafters, can be used to install the back ends of the rafter to the face of the ledger board or directly on the home wall.
- There is also a heavy-duty column anchor system that is a 3” square x ¼” steel post.
- This is used for swing arbors.
- Or for freestanding or attached pergolas to achieve column center spans from center to center to column greater than 18 feet.
- This gives stability to large structures 18 to 22 feet.